A work bench is an important part of a wood workers garage or workshop. It should be sturdy, easy to work with, and help make your shop time more enjoyable.
Here are a few common mistakes you should avoid while designing and building your workbench. I hope this is helpful!
1. Height
Workbench height is critical. Traditionally, people say that the bench height should be even with the knuckles on your hand when your is arm hanging by your side. That may be good for heavy hand work, but for most modern work that is too low. For most operations, the height should be close to waist height. I think my Adjustable Height Workbench is the best of all worlds. I can adjust it high for carving, marquetry, and other detail work. And I can adjust low for hand planning and even lower for assembly work. It is also nice to have an adjustable height bench so that kids, and grandkids, can comfortably work at it, too.
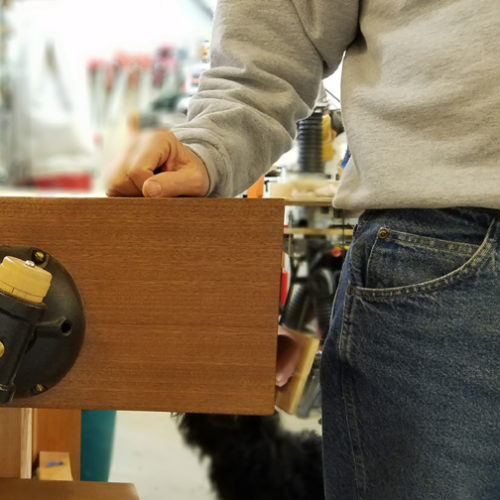
A realistic workbench height is about waist high
2. Wood Types
Many people spend a lot of time worrying about what type of wood to use, when in reality just about any type will be fine. Depending on your needs you could even use plywood, but personally I would not use plywood for the top. You want wood that is affordable, heavy, and easy to obtain. Most importantly, the wood should be dry. Wood that isn’t seasoned tends to warp and is more trouble than it’s worth.
3. The Wrong Vice
You will get used to whatever vise you have, but it’s nice to have a good high quality vise. Personally, I want my main vise to be either fast acting, or quick release. I am also so, so glad that I have an end vise on my bench. It is great for clamping things in between the dog holes. Also consider the type of work that you do. If you do a lot of carving then maybe a dedicated carving vise or even a pattern maker’s vise would be right for you. I get annoyed by people who say that this vise or that bench is the right for everyone. Sure, there are standard vises and standard configurations but it is YOUR bench and you should build it to suit yourself.
4. Dog/Holdfast Holes
Think about your specific end vise before deciding how far to space your dog holes. If you have a fast acting or quick release end vise then you can space the dog holes further apart, maybe 6″ or so. But, if your end vise takes a lot of turns to move a few inches then space them closer together, maybe about 4″ apart.
Holdfast holes are different. Put a few of them where you expect to do most of your work, and drill a few more later if you need them.
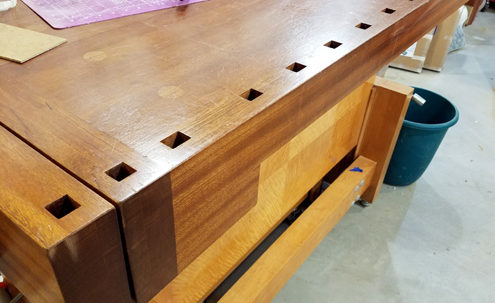
Dog holes spaced fairly close together
5. Waiting For Just The “Right Time”
I am the king of procrastination and sometimes I get analysis-paralysis. I am getting better about this and when I finally do get going I usually realize that I should have just dug in and got started! Don’t get me wrong, I am a big believer in getting your ducks in a row. And, my projects ALWAYS go better when am prepared. The go even better when I draw up a set of plans before starting. What I am saying is Just Do It!
6. Needing to Think I Can’t Build it Without “XYZ” Tool
This is similar to #5, waiting for just the right time. I LOVE tools and the tools available to us are absolutely amazing. As nice as these tools are, you don’t NEED them to great work. People have built great and sturdy workbenches for centuries. Before Festool, before CNC’s, even before electricity. Yes, get the best tools you can afford, but you can do a lot with just an ordinary circular saw.
7. Doing it All Alone
A nice bench can be a big project. My own tendency is to do everything all by myself, and it is hard for me to accept help. But sometimes asking for a little help is the smart thing to do.
8. Stressing about a “Nice” Bench
No matter how beautiful and nice your workbench is, it is still a work bench. This is a place to make beautiful things, not “necessarily” your most beautiful piece of work. When I built my bench I wanted to show it off so I made it beautiful. I’ve never regretted making a nice workbench, but I have to admit that it took me a while before I was able to relax and just use it!
The bottom line is that a sturdy, reliable, and hopefully ergonomic workbench is the foundation of your craft. Have fun and I hope your bench comes out great!
The inspiration for this article was from a guest post that I received from Isaac Atia, author at 10BestRanked, where he reviews the top home and outdoors products.
It is almost a rite of passage that at some point in time a woodworker should construct their own workbench. While it can seem like a bit of a daunting task–especially since you will ultimately rely on it for all of your future woodworking projects–building your own workbench is really the only way to go.
Aside from the fact that you can have pride from having built your workbench by hand, there is a host of other benefits and reasons for why you should build your own workbench. In this article, we will run through some of the best reasons why you should build your own workbench.
Customization
Everyone has their own ideas of what the best workbench should be. While there may be one or two workbenches that you can buy that entice you, chances are there are at least a couple things about the workbench that you would change if you could. Thankfully, if you build your own workbench, that is no longer an issue. By building your own workbench, you are given the freedom to design it however you want.
Workbench Height
It is important that your bench fits you and the way you work. A bench that is too high or too low for you can lead to back aches, or worse. You might consider an Adjustable Height Workbench. Regardless, please be sure that your bench is the right height for YOU.
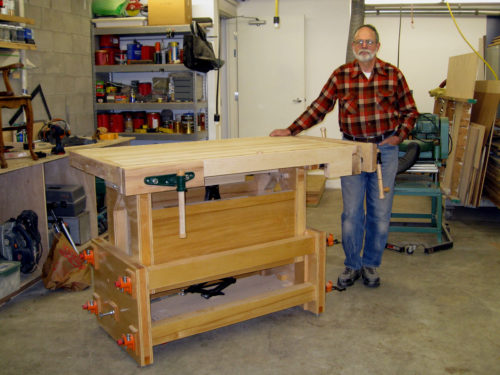
David’s DIY Adjustable Height Workbench
Workbench Size
Not all people have the same amount of space in their workshop. Some people might be lucky enough to have a glut of room in which to work, but most people have to deal with the reality that workshop real estate comes at a premium. Of course, if you build your own workbench, you make it as large or as small as you desire.
Workbench Design
This can be approached from a couple different angles. First, if you are already somewhat of a skilled woodworker, you can ensure that your workbench is truly a piece of art. By adding a number of aesthetic touches, your workbench will stand out as a unique piece that has not been replicated elsewhere. This alone can make the workbench become a family heirloom to be passed down from generation to generation.
Of course, the other primary design benefit to building your own workbench is the fact that it can have whatever additional qualities you decide. If you need more storage space than most workbenches provide, that is no longer an issue. Holes and dowels are also left up to your imagination and the physical limitations of your workpieces. You can also add some genuinely practical and high-quality vices.
Bench Quality
One of the biggest reasons to build your own workbench comes down to craftsmanship. While there are plenty of manufacturers that produce high-end workbenches, they often tend to be well over $100 dollars. Once you start getting too low in price, you find that the quality of the workbench no longer justifies its price. By building it yourself, you can make sure that the workbench maintains a high standard.
Workbench Materials
One of the biggest issues with pre-bought workbenches is that they often use mid to low grade wood unless you are willing to shell out serious cash for quality hardwood. Even then, most pre-made workbenches get their wood from tree farms which rarely allow the wood to fully mature before harvesting it. When you build your own workbench, you are able to make sure you use only the best wood.
Techniques
Even if the company uses a decent quality of wood, that does not guarantee that they use the best techniques to construct or manufacture the workbench. One of the biggest issues with workbenches is that they are often not flat. By making it yourself, you can ensure that the workbench is both stable and flat. You can also go so far as to build it without using hardware to fasten it together–an uncommon practice for prefab workbenches.
Workbench Cost
This one can be a bit hit-or-miss. If you have access to high-grade hardwood that properly matured before being harvested, then it is a no-brainer: it is cheaper to build your own workbench. That said, if your region does not grow top-tier hardwood and you have to purchase imported wood, it will often be similar in price to a prefab workbench.
Practice
The whole point of woodworking is to increase your skill with making wooden projects. What better way to do this than to work on a project that you will use, and what project will you end up using more than a workbench? Not only are you liable to pay close attention to your techniques and craftsmanship, you are likely to learn a great deal about the craft itself along the way.
Conclusion
Whether you want the workbench to be just so or you simply want to make sure that it is exceptionally high-quality, there are plenty of reasons to build your own workbench instead of buying a prefabricated one. On top of the quality and customization, the price of making your own workbench is often less or similar to one that you would purchase.
One thing to remember is that you should build the bench for the woodworker you hope to become not the woodworker that you currently are. Since a solid workbench can last you decades, make sure that the workbench is built for projects you hope to build a decade from now or longer. The best way of doing this is by acquiring a solid set of workbench plans–remember, you can always “improve” on them too.
James Niehaus
A BIG THANKS to Jim at Perfect Cuts and Miters for offering this guest post for the Jack Bench blog page!
Why I Designed this Workbench:
I had a few problems with my first workbench. It was too low for carving or for detail work, it was too high for assembly, it was also too high to sit behind my table saw, and it was difficult to move around. It was anything but ergonomic!
After some thought, I concluded that an Adjustable Height Workbench could solve all of these problems. I then searched the internet to find one. The only option I found was unacceptable to me because it was slow and difficult to actually adjust the height. I decided to design and build one myself, and so my journey began.
The first thing I did was to set some criteria, things that this new bench must have to make it worth the effort. Here is what I came up with:
- First and foremost, it must be a REAL workbench. I wanted an end vise, dog holes, and a nice quick release face vise.
- It would have to have at least 12″ of height adjustability to make it worthwhile.
- It had to be as solid as possible. I would no longer tolerate a bench that moved around while I was working
- It had to be EASY TO USE! I know myself enough to know that if it took more than a few seconds to adjust the height that I would just continue to work in an awkward position until my back gave out. Others might say it’s because I am too lazy, I prefer to think of it as efficient, as in “I can’t waste the time…”.
- It had to be mobile. My shop is small and I have to be able to move things around. And, moving it had to be easy! (see above about laziness, er, efficiency)
The Workbench Design
I had no idea what the bench would look like, but I was determined to meet all of my criteria. I gave this a LOT of thought, in fact, I couldn’t stop thinking about it. My mind went from one idea to another and it kept me up at night, literally. I researched workbenches, I read books and asked other woodworkers what they thought the perfect workbench would look like.
I read books by Scott Landis, Lon Schelling, and Christopher Schwarz. Chris Schwarz’s book is quite good, but it had too narrow of a focus for what I wanted. The Lon Schelling and Scott Landis books are quite similar, but my favorite of the three was The Workbench Book by Scott Landis. The reason I liked this one the best is because he was not stuck on any one particular design. He did not try to say that any one work bench design was best for everyone. What he did instead was to show all sorts of different workbenches and explain their benefits.
After all the research and all the time working on it I finally got a design in my head, but I had to make a cardboard model to see how it would actually go together.
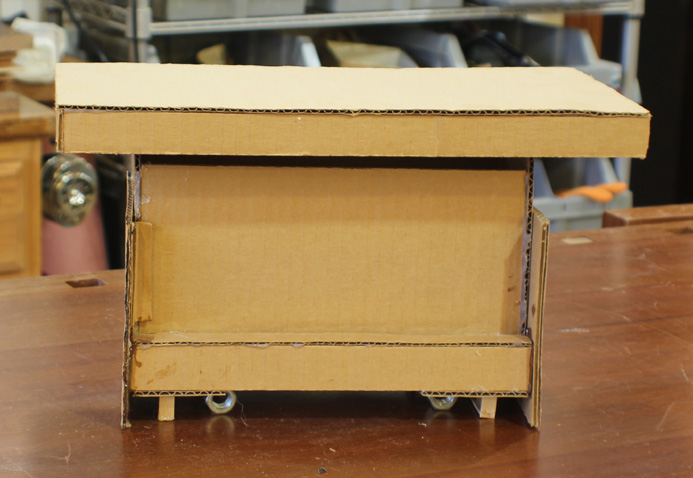
Cardboard Workbench Model
I worked with the model and developed the design until it perfectly met all of my criteria; solid, functional, mobile, ergonomic, easy to operate, and plenty of adjust-ability! What I came up with is a bench with rectangular legs that slid past each other. Some people would describe the legs as “telescoping”. These two sets of legs are held in place with some ordinary pipe clamps. I simply loosen the clamps and adjust the jack to change the bench height. When the bench top is where I want it, I snug up the clamps and the bench is as solid as a rock!
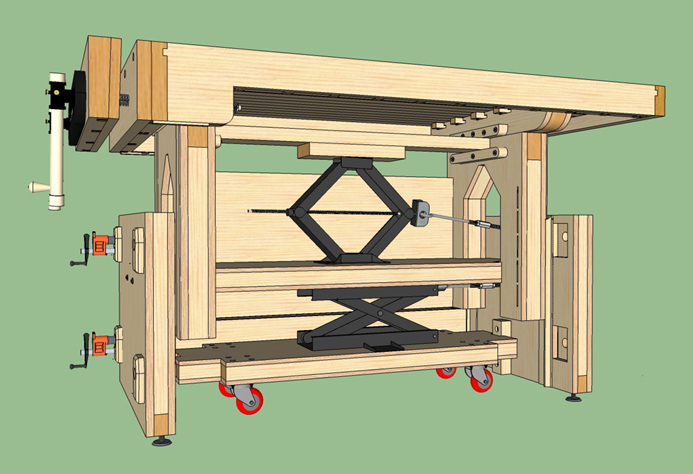
Bench Drawing with Parts Removed for Clarity
You will notice in the drawing above that there are two scissors jacks. The primary jack adjusts the height of the bench top and the other one lifts the entire bench up on to a cart that is nested below the bench.
Actually, if you look closely you will notice that the design in the drawings is slightly different than the design of the bench in the photo. The difference is that the first design, the one in the photo above, has one stretcher and the upper set of pipe clamps go through the inside of the base. On the second, improved design, there are four stretchers and the pipe clamps are concealed inside of them. The revised design is much easier to build than the original one.
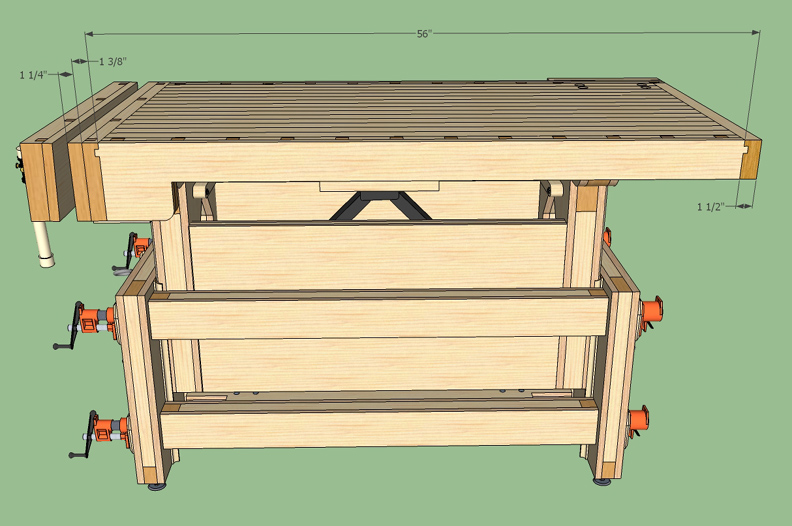
Sketchup Drawing of Jack Bench
The bench top includes everything I wanted, a quick release face vise, bench dogs, and a twin screw vise that doubles as an end vise for the bench dogs.
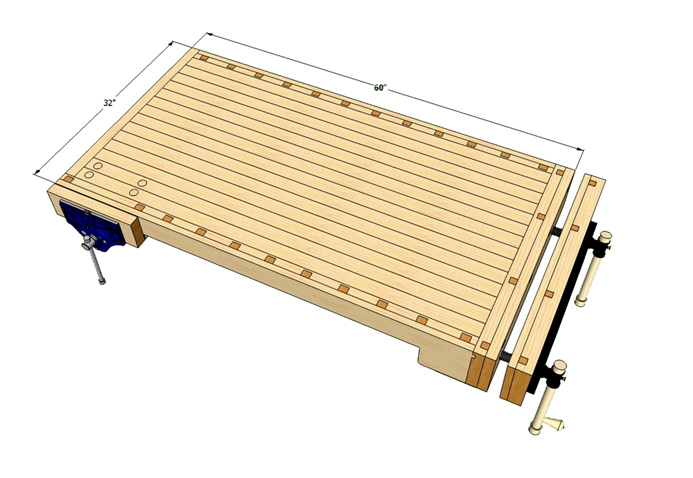
Bench Top Overview
I am thrilled with how the design turned out! I am proud to say that over a thousand people have purchased plans for the Jack Bench since I first designed it. Following are a few photos of benches that others have built from my plans.
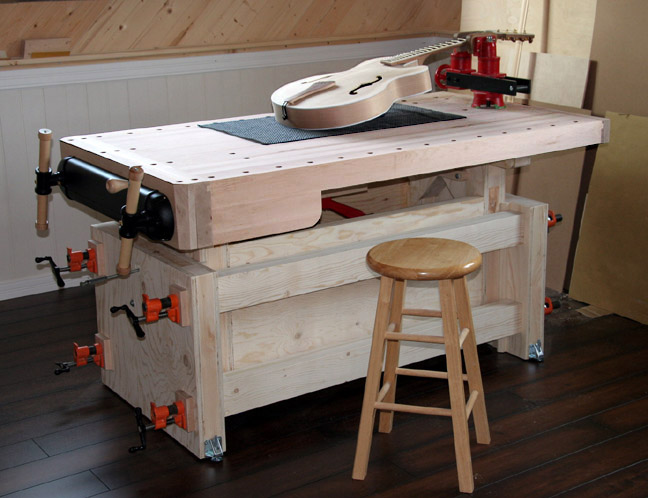
Jack Bench that Serge Lachapelle built from a set of my workbench plans
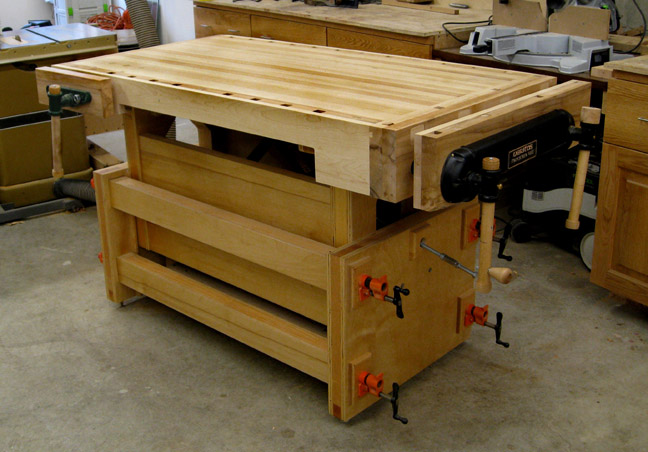
David Root’s Adjustable Height Workbench
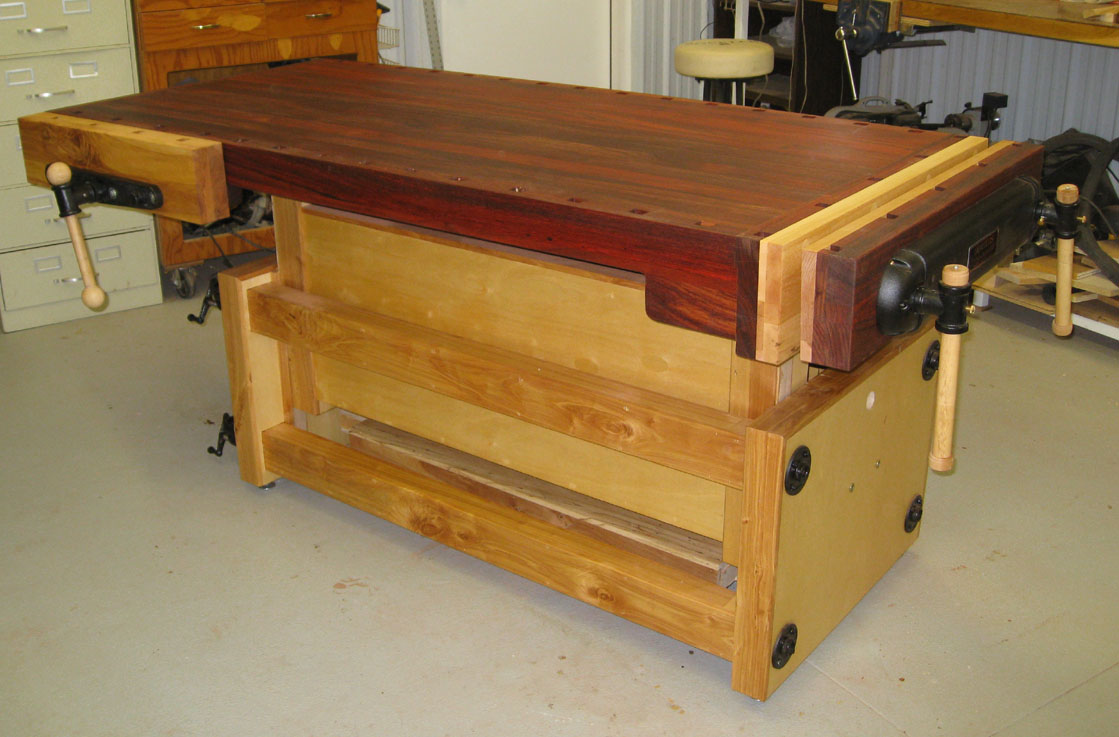
Kevin’s Adjustable Height Workbench
You can see many more examples of benches that others have built from my plans at my photo gallery.
Building a workbench from reclaimed wood is both easy to do and easy on the wallet. You can gain even more in character of appearance if you source reclaimed wood for your project.
While reclaimed wood has grown into a trendy choice for interior decorating, it also makes for some of the best stock on hand for building anything from wooden toys to, as in this case, a sturdy workbench.
There are just a few things about reclaimed wood of which to be aware before you sink any nails or apply the glue.
Hidden Treasure
If you are unfamiliar with reclaimed wood, you might find yourself questioning this choice at first blush. The pieces are hardly smooth or square. It looks like an irregular mess of warped, crooked and rough sawn pieces.
However, when you take a closer look, you begin to notice the aspects of reclaimed wood that makes this source of material very appealing.
Beneath the crusty dirt or chipped and fading paint, through the nails or other metal, beyond the authentic aging and abuse, there is some fine quality wood there.
Depending upon the age and origination, you may have some high-quality, slow-growth stock that stands up to the demands of a reliable workbench.
You Decide: Old or New
With reclaimed wood, you get to make the decision whether you want to maintain its original appearance or take the time to mill the pieces. Beneath what can be considered a clever disguise, there is “good as new” wood just under the surface.
Remembering the fundamentals of a workbench are simple, your approach to preparing your stock should be as well.
Ultimately, the choice of design and degree of intricacy is up to you. Either way, step one is to address cleaning it up.
Cleaning Reclaimed Lumber
Reclaimed timber has trace elements, shall we say? It may have been a barn, at one time, or a gymnasium floor. Between the elements, exposure to natural waste, bugs, the presence of lead paint or chemical treatment typically applied to pallets, you will need to clean this wood.
A stiff brush and compressed air will clean off the finer particles. You can use soap and water to wash the pieces clean. You want to be careful with pressure sprayers to avoid damaging the wood. Using water means you will need to spread the pieces out to thoroughly dry.
Keep in mind, you want to avoid breathing in the sawdust from chemically treated lumber.
Inspect for Hardware
You will want to perform a visual inspection of all the reclaimed pieces to ensure there are no nails, tacks, screws or other remaining hardware and remove as many as you can. It only takes one nail to dull an expensive blade. And let’s be honest, for example in the case of table saws the blade doesn’t cost much but you really don’t want to ruin even a single blade by accidentally running it into a nail.
Urban lumber is notable for its remnant metal. You may appreciate the way the nail holes add character to the wood with their black stains.
Rough around the Edges
Reclaimed stock invariably shows the saw marks from how it was cut. Again, you can choose whether to keep these traces or sand them down. You would be able to mix and match the pieces to accentuate this aspect.
There may be pieces that are thicker at one end or irregular in shape. You can choose to work with these shapes unless you want to do the millwork to make them uniform in appearance. A workbench gets put through the paces anyway.
If the uneven qualities do not interfere with the intended work to be performed on the workbench, these aspects could add to the overall visual appeal.
Locating Reclaimed Lumber
There are numerous sources for reclaimed wood. Start where you are with local connections such as scraps and pallets from shops. Look for those people who specialize in repurposing barn wood or perform urban demolitions. Every time a store is turned over, there is a moment when the interior is remodeled.
In this process, there is a good deal of demolition where lumber might be reclaimed. Keep an eye out for tree trunks from which boards could be cut. You may even know of a neighbor who has a stock pile of logs they plan to get rid of. Just collect all that lumber and start crafting your workbench!
A very special thanks to Paul Stanley at Woodworkboss.com for submitting this great guest posting for the Jack Bench Blog!!
I have two big announcements this week. Neither are directly related to workbenches, but they are both solid woodworking topics! The first is that I finally decided to attend the Woodworking In America Conference held on September 16-18 in Cincinnati, Ohio. This will be the first time I have attended and I am really looking forward to it! Please let me know if you will be there because I would love to have the chance to meet you.
The second big announcement is that I have been invited to be a contributing editor for the Woodworker’s Guild of America! This has been in the works for several months but I have resisted saying anything about it until now. So far, I have produced one video and an accompanying article. They have not released my video yet, so I don’t want to say anything more about it right now. I will let you know more when they release it.
The saga of my broken Ridgid Sander is over. I was ready to hit it with a hammer and throw it in the garbage! It had quit working and it wasn’t a bad cord or a loose connection. The brushes looked good, too. I went on the Home Depot website and all it said was that their power tools came with a 3 year warranty. I received many comments on my YouTube channel saying that Ridgid tools have a lifetime warranty. Obviously, I was skeptical because of what I saw on the HD website. Well! As it turns out, they do have a lifetime warranty IF you send in the registration form, something I almost never do. However, THIS was the exception. Long story short, they fixed my sander for free!
They Fixed My Sander!
I am planning a big road trip on my bike!
Summers in Minnesota are beautiful! They are also very brief. Consequently, I have been spending a lot of my time bike riding. This next weekend I am going on an overnight bike ride with a group of friends. It is 60 miles each day and I am a little worried about that! The longest trip I have taken this year was 37 miles and I was really tired after that. It will be a fun trip regardless and I will let you know how it turns out.
My friend Jeff Hand send me photos of a Z shaped end table that he made.
Jeff Hand
Walnut Slab End Table
Jeff made this from a single walnut slab. He joined the pieces together with large angled dovetails.
Dovetails
He used custom made angled clamping cauls to put it all together.
Angled Clamping Cauls
Dovetails
I want to let you know about a really crazy YouTube video by Peter Brown. Peter comes up with some pretty crazy ideas, but this one was really off the chart. He turned a small piece of wood on his lathe, but he did it using only a strobe light.
A few months ago I made a slab coffee table. It was quite an undertaking and I have 4 other articles on this woodworking project. This video is an overview of the entire build process! This video also includes how I did the copper finish on the base and a bit on how I finished the top of the slab. This article is primarily about how I applied the copper finish on the coopered wooden base.
Before I talk about the finish, let me tell you about the other 4 parts of this build!
The first step in the build of this table was to flatten the slab. I made a simple router jig that worked amazingly well!
The second, and most challenging part of building this table was constructing the coopered “Tree Trunk” base. Although it was challenging it was also a lot of fun!
I love carving! This was far and away the largest carving that I have ever attempted. Sculpting and Texturing with angle grinders was both challenging and fun!
How and Why I Inlaid Stars in the Table Top is a bit of a story! It started because the slab was full of worm holes and I wanted to fill them in.
I tried just filling them with epoxy, but it didn’t look right. (I screwed up) Then, in order to cover the epoxy, I decided to inlay stars in those spots.
OK! Now let me tell you about the faux copper finish!
Initially, I wanted the base to have a bronze finish. This was an easy 2 step process. First I applied a base coat of brown, then I dry brushed a high-quality bronze paint across the top of the texturing.
Applying the brown base coat
Completed Bronze Finish
When I was done the base looked exactly the way I had envisioned. It really looked like a piece of bronze! But, when I set the top onto my beautiful bronze table base there was a big problem. The base had a very green tone and the top had a very red tone. While each of them looked great by itself, they looked terrible when they were together!
The greenish bronze base looked wrong with the reddish slab top
So, being the perfectionist that I am, I brushed another coat of the brown base color over the top of the “bronze” and started over!
Applying 2nd coat of brown
I had 4 different paints. First was the brown base coat, I found that I liked Rustoleum’s satin espresso color the best for this. For the metallic’s it was important to use only the highest quality and I chose “Golden” brand acrylics. The first one I used was an Iridescent Bronze. Then I had two copper colors, Iridescent Copper was more reddish and Iridescent Copper Light was more of a gold colored copper.
It is important to use high-quality paint
First I dry-brushed a coat of the more reddish colored copper paint.
Dry brushing the Red Copper color
But the more I applied the more apparent it was that the red was a bit too red. It seemed to have an artificial look to it.
A little bit too red!
I was glad that I bought both copper colors. To “fix” the too red problem I dry brushed just the slightest bit of the more gold colored paint over the top of the red.
Close up of base after finish was complete
It is not as easy to see in the photos, but adding that little bit of the golden colored copper paint made a BIG difference!
I was very happy with the final result!
Completed Table, compare this to how it looked with the bronze colored base!
Check out the accompanying articles about this table
Andy Klein is an amazingly creative person. He has 5 patents for various different woodworking related inventions, and certainly there will be more! His most successful invention so far is a saw blade that allows you to make a box on your table saw like magic. His saw blade invention is now fully developed and will be available through a major woodworking retailer sometime in 2017.
Andy Klein
He is currently trying to find manufacturing and/or retail partner to make two of his other inventions available to the public.
The first of them is new kind of parallel clamp. This new clamp does everything that a regular parallel clamp does AND it can also function as a panel clamp. If you have ever had a panel bow up when you tried clamped the pieces together then you would love this one! I don’t have a good picture of his revised design, but I would encourage you to watch the video that he made about it:
A friend of mine saw a bookcase in a woodworking magazine. She knows all about my workbench and my woodworking YouTube videos so she knew that this would be an easy project for me. So, she asked me to make one for her grandchildren.
Gluing the apron and the cleats on to the top
Her grandchildren, Billy and Alex live in another state with their mother and my friend was going to deliver the bookcase to them. Actually, that was my biggest challenge on this project because she was leaving in 2-1/2 days so this was definitely a rush job! After I agreed to do it, she asked me if I could make 2 of them. I try to be a nice guy, but I couldn’t commit to 2 bookcases in 2 days!
Test fitting the pieces
She wanted the boys to be involved in construction of the bookcase, so I had to build it as a kit rather than a finished piece. I had this in the back of my mind the whole time I was building it and I made sure that assembly would be easy and as fool proof as possible.
Zippy with the bookcase before I disassembled it and sent it off to the boys for finishing
I don’t normally work from plans in magazines, but having the dimensions all laid out for me did make it a lot easier! Of course, I did stray just a bit from the original plan. The plan in the magazine called for solid wood construction and used a combination of pocket screws and dado joints. I kept the dado joints, but ditched the pocket screws. I also made it from cherry plywood and added solid cherry edge-banding. Also, the one in the magazine had 3 shelves and I made this one with 4 shelves so it is taller than the one in the magazine.
After the boys got it they glued it and clamped it together, they nailed the back on and they applied a wipe on polyurethane finish.
It turned out quite well, especially since it was such a rush job!
Billy and Alex with completed bookcase
Just about all of us have a circular saw in our workshop, but most of us call them Skillsaws! These handy little saws have been around since before we were born. The name Skillsaw is a synonymous with circular saws as Kleenex is to tissues. We buy them, we use them, and we love them. Unfortunately, very few of these saws allow for any dust collection and the ones that do are either hard to find and/or very expensive.
That is a real shame because managing wood dust and keeping it out of your lungs is pretty important. None of us want to end up dragging an oxygen bottle around!
I found a very easy way to add a dust fitting to just about any circular saw. My Skillsaw came with a hole toward the back of the shroud around the blade where the dust shoot out. My solution was simply to epoxy a small plastic dust fitting over the hole in the shroud.
Skillsaw with dust collection
Dust Port on Circular Saw
Adding the dust fitting to my circular saw was very easy.
Dust Port on Circular Saw
I was able to substantially upgrade my circular saw for less than five dollars!
Dust fitting on Skillsaw
OK, so the obvious question is “how well does it work?”. I would be lying if I said that it was as good as a one of the high end saws like a Festool. But, a Festool will cost somewhere in the neighborhood of $600. If you can afford that, or if you use your saw very frequently then by all means buy a saw with excellent dust collection. On the other hand, if you can’t justify big money for a saw that you use only once in a while then this little upgrade is a no brainer!